INICIO / NOTICIAS / Noticias de la Industria / ¿Qué medidas se toman para abordar los problemas relacionados con la prevención de la corrosión y el óxido en piezas de chapa, especialmente al aire libre o en entornos hostiles?
Abordar la prevención de la corrosión y la oxidación en piezas de chapa metálica, particularmente en ambientes exteriores o hostiles, implica una combinación de selección de materiales, tratamientos superficiales y revestimientos protectores. Estos son los pasos que se toman comúnmente:
Selección de materiales: participar en pruebas exhaustivas de corrosión, incluida la exposición a condiciones ambientales simuladas y pruebas de envejecimiento acelerado, para validar el rendimiento previsto de los materiales seleccionados. Colabore con metalúrgicos e ingenieros de materiales para analizar las propiedades microestructurales, garantizando que la aleación elegida no solo resista la corrosión sino que también mantenga la integridad mecánica bajo tensión.
Tratamientos Superficiales: Implementar metodologías de control estadístico de procesos (SPC) para monitorear y optimizar los parámetros de los procesos de tratamiento superficial, minimizando variaciones y asegurando una calidad consistente. Utilice técnicas avanzadas de espectroscopia y análisis de superficies, como la espectroscopia de fotoelectrones de rayos X (XPS), para caracterizar con precisión la composición y el espesor de las capas de óxido.
Recubrimientos protectores: invierta en tecnologías de recubrimiento de vanguardia, como recubrimientos de nanocompuestos o recubrimientos autorreparables, para proporcionar una mayor resistencia contra la corrosión y la degradación ambiental. Realice pruebas de intemperismo acelerado para simular la exposición a largo plazo a la radiación UV, la humedad y las fluctuaciones de temperatura, asegurando la durabilidad de los recubrimientos protectores.
Galvanización: Implementar líneas de galvanizado controladas por computadora con sistemas automatizados de monitoreo de espesor, permitiendo ajustes en tiempo real para lograr el espesor de recubrimiento de zinc deseado. Integre robótica e inteligencia artificial para mejorar la precisión del proceso de galvanizado, reduciendo el error humano y garantizando una distribución uniforme del recubrimiento.
Anodizado (para aluminio): emplee técnicas de anodizado por pulsos para lograr propiedades superiores de la capa de óxido, incluida una mayor dureza y una mejor resistencia a la corrosión. Utilice herramientas de monitoreo in situ, como la espectroscopia de impedancia, para evaluar continuamente la integridad de la capa anodizada durante el proceso.
Protección catódica: Implemente sistemas de monitoreo avanzados que se integren con sistemas de control de supervisión y adquisición de datos (SCADA) para el análisis en tiempo real de la efectividad de la protección catódica. Utilice algoritmos de aprendizaje automático para predecir y abordar de forma preventiva posibles fallos en sistemas de protección catódica basándose en datos históricos de rendimiento.
Consideraciones de diseño: utilice simulaciones de dinámica de fluidos computacional (CFD) para optimizar el diseño del drenaje, garantizando que el agua no se acumule en áreas críticas. Emplee algoritmos de optimización de topología para refinar la geometría de las piezas de chapa, minimizando las concentraciones de tensión y las áreas propensas a la corrosión.
Inspección y mantenimiento periódicos: implementar tecnologías de inspección automatizadas, como drones equipados con sensores de monitoreo de corrosión, para acceder y evaluar piezas de chapa en entornos desafiantes o peligrosos. Integre algoritmos de mantenimiento predictivo que analicen datos históricos de inspección para pronosticar y programar actividades de mantenimiento de manera proactiva.
Sellos ambientales: participar en investigaciones colaborativas con instituciones de ciencia de materiales para desarrollar sellos personalizados con propiedades químicas y físicas adaptadas a entornos específicos. Implementar pruebas de envejecimiento acelerado en los sellos para evaluar su desempeño a largo plazo en condiciones ambientales adversas.
Pruebas y control de calidad: utilice métodos de prueba no destructivos, como pruebas de corrientes parásitas o pruebas ultrasónicas para detectar la corrosión del subsuelo o la degradación del material. Implemente sistemas automatizados de control de calidad que aprovechen la visión artificial y la inteligencia artificial para identificar y categorizar defectos superficiales, garantizando estándares de alta calidad.
Procesamiento de chapa metálica OEM Doblado Punzonado Proceso de fabricación Corte por láser Fabricación de estampado
Procesamiento de chapa metálica OEM Doblado Punzonado Proceso de fabricación Corte por láser Fabricación de estampado
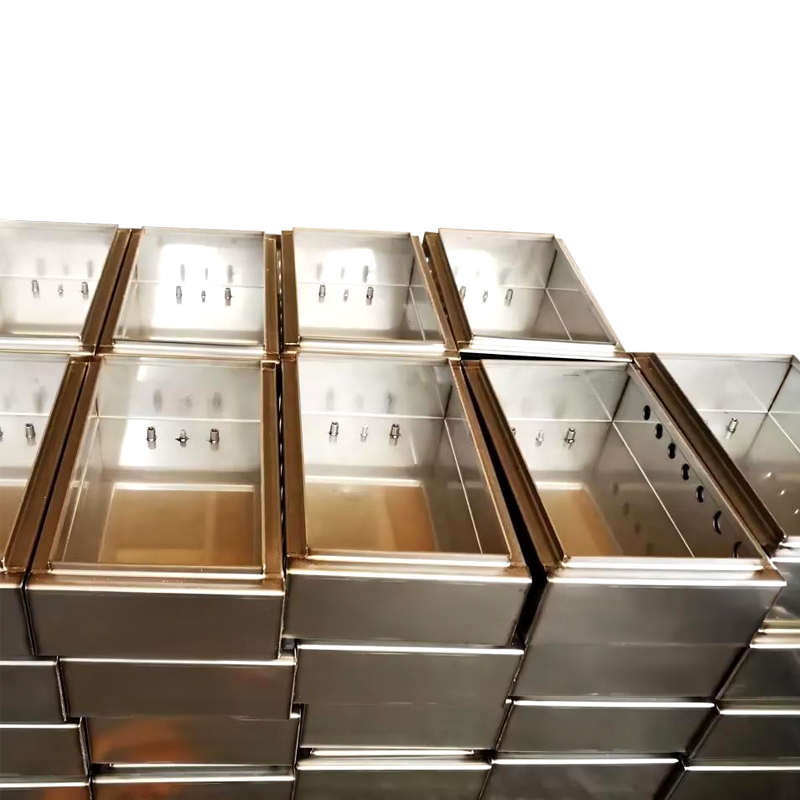